What fire protection should you have in place to help prevent a fire at an electricity substation? Joshua Slack, National Specification Manager for passive fire protection experts, Promat, shares his advice.
Substations are a vital component of the country’s national electrical grid with more than 400,000 sites operating across the UK today. Their efficient operation is crucial to ensuring a continuous and reliable power supply to both homes and businesses. A fire can cause significant damage to equipment and infrastructure which can create prolonged outages and bring about huge commercial losses for the owner operator – as well as energy instability for local communities.
This was no more evident than the major fire that occurred at the Sellindge substation in Kent in 2021, which caused power outages in the UK and France.
Clearly, avoiding the occurrence of fire at all should be the primary concern of substation designers and operators, but this can never be 100% successful. So, it is vital that the role of passive fire protection is fully considered in helping to limit the spread of fire or smoke should the worst happen.
Ultimate protection
Substations house a wide range of electrical equipment, including transformers, switchgear, and control systems which can generate a large amount of heat during normal operation. Faults or malfunctions in these systems can cause electrical arcing, which can ignite combustible materials, such as oil, gas, or insulation materials. Additionally, external factors such as lightning strikes or accidental contact with metallic objects have historically caused fires in power facilities.
Passive fire protection provides an important complement to active systems – such as fire alarms, extinguishers and automated doors – by protecting key structural parts of a building from failure and buying valuable time before fire can reach critical assets or vessels within a plant. This generally comprises the installation of fire-resistant insulation boards that are fitted directly to the steel support structures within a facility, as well as fire walls where it has been decided that areas should be compartmentalised.
The other key component that requires consideration with substations, is blast protection. Combining passive fire protection alongside the ability to withstand impact from shrapnel, over and under pressures can be extremely difficult to achieve.
Designing for the situation
It’s important to bear in mind that no two substations are the same, so having a bespoke passive fire protection system is essential, considering how the most robust and effective protection can be achieved.
An important factor in deciding which system is most appropriate for fire protection is the likely duration of the exposure to fire. Typically, substations require passive fire protection that can last four hours – it’s hoped that the fire service would have been able to deal with the fire within that time.
Choice of products
So, which products should you choose? There are several types of passive fire protection solutions to choose from, including cementitious sprays and intumescent coatings through to calcium silicate and specialist impact cement boards.
Systems based on coatings are normally mixed – depending on the application – and sprayed onto the surface. These can be prone to damage when impacted and require onerous inspection and maintenance regimes, therefore whilst the upfront cost may be low, the cost over the life of the project may be high. The fire-resistant performance of the coatings is dependent on the thickness of the coating, and they are only used to protect structural elements and not to compartmentalise buildings.
On the other hand, calcium silicate boards can be used both for structural protection and compartmentation. These are durable, ‘fit and forget’ products which can provide high levels of fire resistance and so are often used in high value or high-risk buildings such as substations. The protective capability of the system is provided by its excellent integrity and ability to insulate against extreme temperatures.
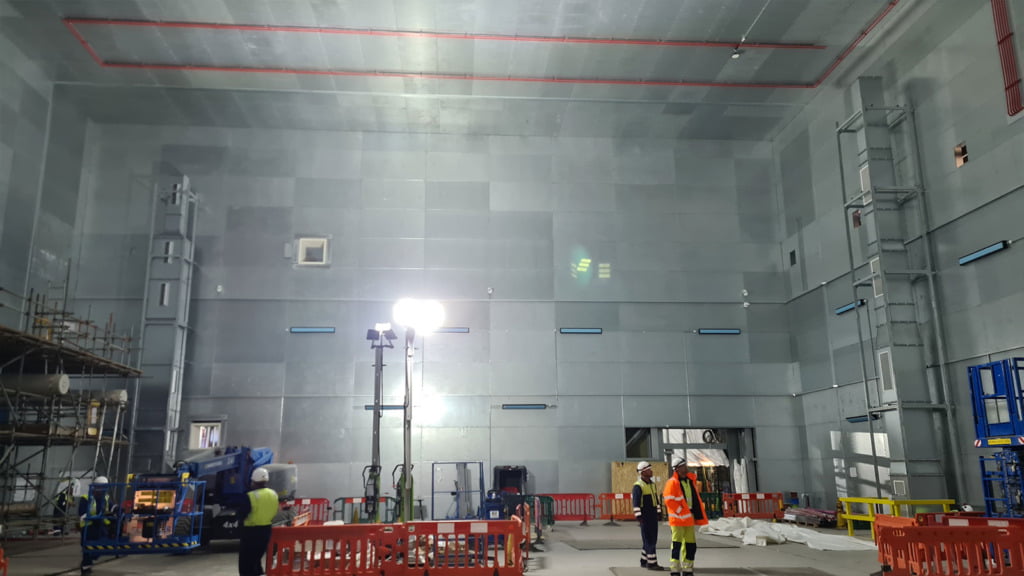
Performance testing
It’s imperative that operators have detailed information from the supplier or manufacturer of the passive fire protection products and systems installed – this is vital evidence that the fire protective products used meet defined performance criteria based on standard (third party) tests that replicate the fire conditions.
Typically, there are three main criteria to classify a system by, integrity, insulation, and load-bearing capacity.
- Integrity is about maintaining the separating function and preventing the spread of flame and smoke.
- Insulation is based around the premise that the surface protected will not reach an average temperature rise of 140°C above ambient, with no-one one hot spot exceeding 180°C above ambient.
- Finally, load-bearing capacity relates to the structural element being able to support the load under fire.
The performance of some passive fire protection systems, such as reactive coatings, can deteriorate over time, while some plant operational and maintenance activities can damage or eradicate its capabilities. Additionally, the protected surface itself can corrode underneath the fire protective barrier – so it’s important to put procedures in place to ensure that both the passive fire protective system and the protected surface are regularly inspected and repaired as appropriate. Alternative technologies, such as boarded systems, tend to require less inspection and maintenance.
Resolving Sellindge’s fire protection problems
In the case of the Sellindge substation in Kent, it has since received a fire protection overhaul, with a detailed specification plan that offered optimum protection by using a combination of products to meet the scale of the facility – which has some halls reaching up to 16 metres in height.
The package that was installed included a highly protective composite impact board, that could be used at the heights required, with a fibre reinforced concrete core and galvanised steel out facings, designed to offer the highest level of fire resistance with exceptional robustness for constructing fire compartmentation. Additionally, this board can provide blast protection, to ensure that if the electrical equipment were to fail and cause an explosion, the passive fire protection would not be compromised, and the fire can be contained.
The project also used a non-combustible calcium silicate board to provide up to 240 minutes of fire protection for the structural steel at the plant, to maintain load bearing capacity when exposed to fire.
The combination of these two high performance products means that Sellindge can now benefit from a comprehensive fire protection system that ensures excellent protection from both the spread of fire and the risk it could pose to the structural integrity of the building.