The lighting industry is starting to embrace the concept of the circular economy and sustainable lighting. Nigel Harvey, CEO of Recolight, outlines the need for sustainable lighting and initiatives that we’re seeing now.
Legislative changes and customer requirements are increasingly placing an emphasis on lighting that is truly sustainable – products that are not just energy efficient, but which are also resource efficient. These are vital steps in addressing the climate emergency.
The circular economy is about resource efficiency; minimising the use of new raw materials in products, and keeping products in service for far longer. Value engineered products that compromise longevity and are unlikely to last much beyond their warranty period should be avoided. That’s because they risk creating unnecessary waste, the requirement for early replacement, and carry a higher embodied carbon.
Choosing resource efficient products is paramount. There are many potential benefits, including the fact that many resource efficient products benefit from modular design, meaning they could feature replaceable light sources and control gear. This means that if one critical component fails in use, the component can be replaced without having to replace the whole fitting.
Legislation and specifications
To help identify more sustainable products, the Society of Light & Lighting and CIBSE have come up with a new rating dubbed TM66, which many manufacturers are now showcasing on their products. TM66 helps lighting producers demonstrate the extent to which they have taken circular economy principles into account in product design. Products are rated on a 0-4 scale, which is assessed based on the product’s sustainability across four key tenets:
- Product Design: covering topics such as design for long life and repair.
- Materials: covering topics like usage of recyclable materials rather than virgin.
- Manufacturing: covering topics like additive and subtractive techniques and localisation.
- Ecosystem: covering topics like repair or upgrade services to complement circular economy design and manufacturing.
By asking for, and promoting products with a TM66 rating, specifiers are able to encourage end users to fit products that will be more resource efficient. This is obviously beneficial to a project’s carbon footprint, but could also prove fruitful for the client’s bottom line.
Efforts to improve circularity within the lighting industry don’t stop at TM66, with a BSI committee currently working on a lighting version of BS8887, a standard for the remanufacture of luminaires. This standard will help companies remanufacture in a way that applies realistic approaches to product compliance and will give end users the confidence that the product is suitable for use.
Additionally, legislative changes are expected to encourage or require manufacturers to take greater responsibility for waste products from business customers, via their WEEE compliance scheme. This may include requiring producers to finance the free of charge collection and recycling of WEEE from businesses, subject to minimum quantities. Schemes, like Recolight, already operate in this way, but there are still many schemes that do not.
Changes to legislation may also incentivise manufacturers to prioritise the repair and upgrade of older products, rather than the manufacture and supply of new products.
Remanufacturing lighting
One of the biggest barriers to the re-use of lighting equipment is the perception that customer demand is limited. However, clients, both corporate and public sector, are now warming to the concept of reconditioned lighting to achieve both sustainability goals and cost savings. And now tenders are beginning to emerge which specify the reconditioning and re-use of luminaires in a project. The more end users include re-used or remanufactured products as an option in specifications, the more we will see producers offering these solutions.
In fact, an increasing number of lighting manufacturers also now offer to upgrade existing lighting products to LED. These upgrades can sometimes be performed in situ, without the need for the fittings to return to a factory. That means the fittings and/or their housings themselves can be kept in service. That in turn improves material efficiency, and should avoid the loss of much of the embodied carbon. This approach can also be commercially attractive – there have been great examples of remanufactured products that are more cost effective, and more energy efficient for the end user, and with better margins for the producer.
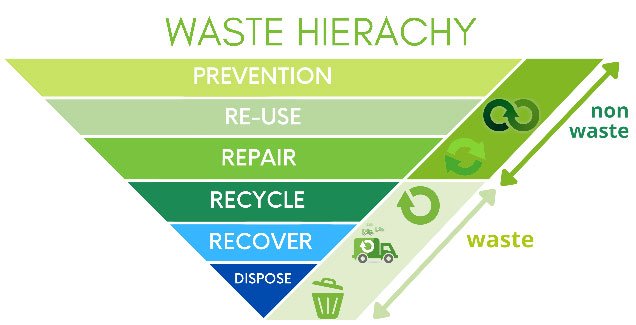
Applying the waste hierarchy for lighting
All too often we think that getting products recycled means we have ‘done our bit’ for the environment. We need to change that mentality. The waste hierarchy quite rightly puts recycling below prevention, repair, and re-use. Recycling destroys most of the embodied carbon in an electrical product, and should only be used if re-use, repair and remanufacture are not possible. To drive improved sustainability in the lighting sector, we must get much better at applying the waste hierarchy. That means prioritising repair and re-use above recycling.
Of course, re-use is not always possible, as is certainly the case for waste lamps. In this instance, they should be collected and properly recycled. That’s why WEEE compliance schemes exist – they can help to responsibly deal with these products at the end of their life. Some, like Recolight, will even offer a free of charge waste lamp collection and recycling service, subject to minimum quantities.
Furthermore, where luminaires supplied are produced by a member, the WEEE scheme may also be able to provide a free recycling service for any waste fittings that arise. But as has been previously highlighted, this should be a last resort – it’s imperative to prioritise re-use first. The relevant WEEE scheme may be able to find a company willing to receive these products for remanufacture, avoiding unnecessary recycling.