Vestas has unveiled a brand-new chemical process that could lead to all wind turbine blades becoming recyclable.
While being able to recycle wind turbine blades is nothing new, it previously required blades to be engineered with specific materials. Take Siemens Gamesa’s RecyclableBlade, it was the first commercial blade to offer a comprehensive recyclable solution, but it was a specific product that businesses had to buy — it still meant existing blades and products from Siemens Gamesa’s competitors would end up in landfill.
That’s why Vestas’ revelation is a little more interesting, it removes the need to buy a specific product, or changes the design or composition of the materials used for wind turbine blades. Instead, through a special chemical process, all epoxy-based blades can be broken down into their raw material that can be reused to make new wind turbine blades, or for other purposes.
Vestas, as well as its partners Aarhus University, Danish Technological Institute, and epoxy maker Olin, discovered the chemical process as part of a coalition set up in May 2021, dubbed the CETEC project – Circular Economy for Thermosets Epoxy Composites. Having successfully demonstrated its abilities, the companies now plan to scale the process.
Lisa Ekstrand, Vice President and Head of Sustainability at Vestas, noted, “Until now, the wind industry has believed that turbine blade material calls for a new approach to design and manufacture to be either recyclable, or beyond this, circular, at end of life. Going forward, we can now view old epoxy-based blades as a source of raw material.
“Once this new technology is implemented at scale, legacy blade material currently sitting in landfill, as well as blade material in active wind farms, can be disassembled and reused. This signals a new era for the wind industry, and accelerates our journey towards achieving circularity.”
To scale up the process, Vestas is partnering with Nordic recycling firm Stena Recycling and Olin.
“In the coming years, thousands of turbines will be decommissioned or repowered, representing a major sustainability challenge but also a valuable source of composite materials”, commented Henrik Grand Petersen, Managing Director at Stena Recycling Denmark.
“We see this solution as a huge opportunity to take part in making a sustainable solution even more sustainable and circular and are ready to apply our chemical recycling expertise and knowledge to this process.”
The ability to recycle all wind turbine blades will be a major win for the wind power industry, which has previously been criticised by campaigners as not being as ‘green’ as it claims to be due to the amount of waste produced at the end of a wind turbine’s life.
In fact, to put things into perspective, WindEurope expects around 25,000 tonnes of blades to read the end of their operational life annually by 2025, rising to 52,000 tonnes by 2030. Being able to recycle those blades will have a major impact on the circularity of the industry — meaning this discovery from Vestas has the potential to be absolutely huge, provided it works at scale, of course.
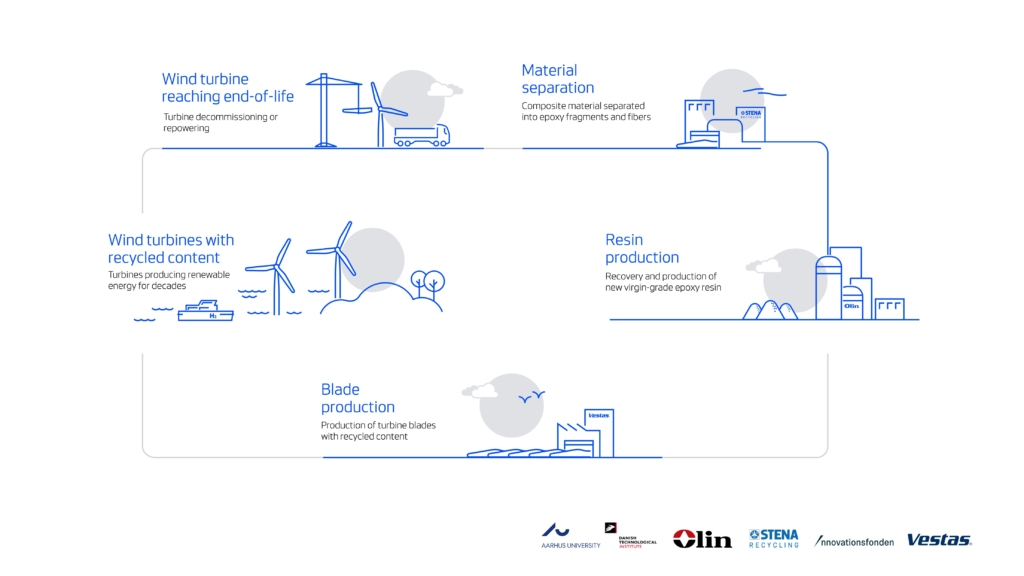